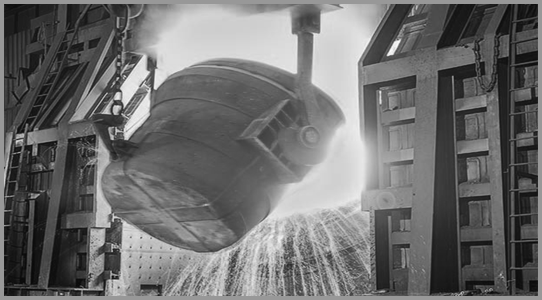
فهرست مطالب
انواع کوره های تولید آهن و بررسی آنها
آهن، یکی از مهمترین فلزات مورد استفاده در دنیا، نقش حیاتی در صنایع مختلف از جمله ساختمان سازی، خودروسازی و لوازم خانگی ایفا می کند. فرآیند تولید آهن شامل مراحل مختلفی است که ذوب سنگ آهن و تبدیل آن به چدن مذاب یکی از مراحل کلیدی آن به شمار می رود. در این مرحله از کوره های مختلفی استفاده می شود که هر کدام مزایا و معایب خاص خود را دارند. در این مقاله به بررسی 1000 کلمه ای انواع کوره های تولید آهن و عملکرد هر یک می پردازیم.
1. کوره بلند:
کوره بلند، قدیمی ترین نوع کوره برای ذوب سنگ آهن است که قدمت آن به چندین هزار سال قبل باز می گردد. این کوره ها از آجرهای نسوز ساخته شده و ارتفاع آنها می تواند به 30 متر و قطر آنها به 10 متر برسد. سوخت اصلی کوره بلند کک است که از زغال سنگ به دست می آید.
نحوه عملکرد:
- سنگ آهن به همراه مواد احیا کننده (کک) و شار (آهک) به طور پیوسته از طریق قسمت بالایی کوره به داخل آن ریخته می شود.
- با احتراق کک، گرمای شدیدی در کوره ایجاد می شود که باعث ذوب شدن سنگ آهن و احیای آن به آهن می شود.
- ناخالصی های موجود در سنگ آهن به همراه شار ذوب شده و به صورت سرباره از کوره خارج می شوند.
- چدن مذاب حاصل از ذوب سنگ آهن در قسمت پایینی کوره جمع آوری و از طریق دریچه ای تخلیه می شود.
مزایا:
- ظرفیت تولید بالا
- قابلیت استفاده از سنگ آهن با کیفیت پایین
- هزینه ساخت و نگهداری نسبتا پایین
معایب:
- مصرف سوخت بالا و آلودگی زيست محيطی زیاد
- راندمان پایین
- تولید گازهای گلخانه ای
2. کوره قوس الکتریکی:
کوره قوس الکتریکی، نوعی کوره ذوب است که از انرژی الکتریکی برای ذوب مواد استفاده می کند. این کوره ها به دو دسته کلی AC و DC تقسیم می شوند.
نحوه عملکرد:
- قراضه آهن به همراه مواد افزودنی (آهک، دولومیت و …) به داخل کوره شارژ می شود.
- الکترودهای کربنی که از سقف کوره آویزان هستند، جریان الکتریکی را به داخل کوره هدایت می کنند.
- قوس الکتریکی بین الکترودها و مواد داخل کوره ایجاد شده و گرمای شدیدی تولید می شود.
- با افزایش دما، مواد داخل کوره ذوب شده و به چدن مذاب تبدیل می شوند.
- سرباره حاصل از ذوب ناخالصی ها از چدن مذاب جدا شده و از کوره خارج می شود.
مزایا:
- راندمان بالا و مصرف انرژی پایین
- قابلیت کنترل دقیق فرآیند ذوب و تولید فولاد با کیفیت بالا
- قابلیت استفاده از انواع مختلف مواد اولیه
- آلودگی زیست محیطی کمتر نسبت به کوره بلند
معایب:
- هزینه ساخت و نگهداری بالا
- نیاز به برق با ولتاژ بالا
- تولید گازهای گلخانه ای
3. کوره کنورتور اکسیژن پایه (BOF):
کوره کنورتور اکسیژن پایه، نوعی کوره ذوب است که از اکسیژن به عنوان عامل اکسنده برای تصفیه چدن مذاب استفاده می کند.
نحوه عملکرد:
- چدن مذاب حاصل از کوره بلند یا کوره قوس الکتریکی به داخل کوره BOF ریخته می شود.
- اکسیژن با فشار بالا از طریق نازل هایی به داخل کوره تزریق می شود.
- اکسیژن با ناخالصی های موجود در چدن مذاب (مانند کربن، سیلیسیم، منگنز و فسفر) واکنش داده و آنها را به اکسید تبدیل می کند.
- اکسیدهای ناخالصی ها به همراه مواد افزودنی (آهک و دولومیت) به صورت سرباره از کوره خارج می شوند.
- فولاد مذاب تصفیه شده از کوره تخلیه و برای مراحل بعدی فرآوری مانند نورد و ریخته گری ارسال می شود.
مزایا:
- راندمان بالا و سرعت ذوب سریع
- قابلیت تولید فولاد با کیفیت بالا
- مصرف انرژی نسبتا پایین
معایب:
- نیاز به چدن مذاب با کیفیت بالا به عنوان مواد اولیه
- تولید گازهای گلخانه ای
- آلودگی صوتی بالا
4. کوره قوس الکتریکی (EAF) با روش AOD
کوره قوس الکتریکی (EAF) با روش AOD (Argon Oxygen Decarburization) نوعی کوره ذوب است که از ترکیب کوره قوس الکتریکی و فرآیند تصفیه با اکسیژن و آرگون برای تولید فولاد با کیفیت بالا استفاده می کند.
نحوه عملکرد:
- چدن مذاب حاصل از کوره قوس الکتریکی به داخل کوره AOD منتقل می شود.
- مخلوطی از گازهای اکسیژن و آرگون از طریق نازل هایی به داخل کوره تزریق می شود.
- اکسیژن با ناخالصی های موجود در چدن مذاب (مانند کربن، سیلیسیم، منگنز و فسفر) واکنش داده و آنها را به اکسید تبدیل می کند.
- آرگون به عنوان گاز حامل عمل می کند و به هم زدن مذاب و جداسازی اکسیدها از فولاد کمک می کند.
- اکسیدهای ناخالصی ها به همراه مواد افزودنی (آهک و دولومیت) به صورت سرباره از کوره خارج می شوند.
- فولاد مذاب تصفیه شده از کوره تخلیه و برای مراحل بعدی فرآوری مانند نورد و ریخته گری ارسال می شود.
مزایا:
- قابلیت تولید فولاد با کیفیت بسیار بالا با ناخالصی های بسیار کم
- کنترل دقیق فرآیند تصفیه و تولید فولاد با خواص مورد نظر
- راندمان بالا و مصرف انرژی نسبتا پایین
معایب:
- هزینه ساخت و نگهداری بالا
- نیاز به چدن مذاب با کیفیت بالا به عنوان مواد اولیه
- تولید گازهای گلخانه ای
5. کوره قوس الکتریکی خلا (Vacuum Arc Remelting – VAR):
کوره قوس الکتریکی خلا (VAR) نوعی کوره ذوب است که از ترکیب کوره قوس الکتریکی و خلا برای تولید فولاد با کیفیت فوق العاده بالا استفاده می کند.
نحوه عملکرد:
- شمش های فولادی به داخل محفظه کوره که از هوا تخلیه شده است، قرار داده می شوند.
- الکترودهای کربنی که از سقف کوره آویزان هستند، جریان الکتریکی را به داخل کوره هدایت می کنند.
- قوس الکتریکی بین الکترودها و شمش های فولادی ایجاد شده و گرمای شدیدی تولید می شود.
- با افزایش دما، شمش های فولادی ذوب شده و به فولاد مذاب تبدیل می شوند.
- خلا موجود در کوره باعث می شود که گازهای موجود در فولاد مذاب خارج شده و ناخالصی های آن به حداقل برسد.
- فولاد مذاب تصفیه شده به داخل قالب های ریخته گری ریخته شده و پس از سرد شدن به شمش های فولادی با کیفیت فوق العاده بالا تبدیل می شود.
مزایا:
- قابلیت تولید فولاد با کیفیت فوق العاده بالا با حداقل ناخالصی
- کنترل دقیق فرآیند ذوب و تولید فولاد با خواص مورد نظر
- راندمان بالا و مصرف انرژی نسبتا پایین
معایب:
- هزینه ساخت و نگهداری بسیار بالا
- سرعت ذوب پایین
- نیاز به شمش های فولادی با کیفیت بالا به عنوان مواد اولیه
انتخاب نوع کوره:
انتخاب نوع کوره برای تولید آهن و فولاد به عوامل مختلفی از جمله کیفیت مواد اولیه، ظرفیت تولید، هزینه ساخت و نگهداری، کیفیت فولاد مورد نظر و الزامات زیست محیطی بستگی دارد.
- کوره بلند برای تولید انبوه آهن با کیفیت پایین مناسب است.
- کوره قوس الکتریکی برای تولید فولاد با کیفیت بالا از قراضه آهن یا چدن مذاب استفاده می شود.
- کوره BOF برای تصفیه چدن مذاب و تولید فولاد با کیفیت بالا به کار می رود.
- کوره AOD برای تصفیه نهایی فولاد و تولید فولاد با کیفیت بسیار بالا استفاده می شود.
- کوره VAR برای تولید فولاد با کیفیت فوق العاده بالا با حداقل ناخالصی به کار می رود.
نتیجه گیری:
انواع مختلفی از کوره ها برای تولید آهن و فولاد وجود دارد که هر کدام مزایا و معایب خاص خود را دارند. انتخاب نوع کوره مناسب به عوامل مختلفی بستگی دارد که در این مقاله به آنها اشاره شد.
امیدواریم این مقاله اطلاعات مفیدی در مورد انواع کوره های تولید آهن و بررسی هر کدام ارائه کرده باشد.
برای مشاهده محصولات کیان آهن روی لینک زیر کلیک کنید.